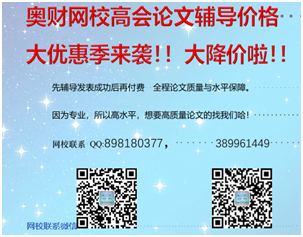
山東新華制藥股份有限公司(以下簡稱新華制藥)自2007年1月開始ERP二期項目中的成本模塊實施,經過系統調研、系統培訓、系統定義、數據準備、系統切換、系統上線維護6個階段,至2008年9月完成預定目標,項目進入正常運行維護階段。通過二期項目的實施,新華制藥將信息化管理深入到車間現場,能夠進行原料、產品的批次追蹤查詢、產品成本查詢,完善了原料藥生產成本管理考核體系,并與物流、檢驗、財務等系統無縫集成,形成了完整的ERP應用模式,覆蓋了產品銷售訂單、需求預測、產品銷售、產品生產、原材料采購、成本核算等企業管理的全過程。但同其他企業一樣,新華制藥ERP的實施也不是一帆風順的。
一、實施難點和解決途徑
(一)人為因素導致錯誤百出
成本模塊上線之后的前幾個月的成本計算出現了大量的錯誤,有的成本翻了一倍還多,主要原因有:一是人員操作上存在問題。主要表現在初始化數據不正確、公司倉庫物料調撥不及時、車間人員數據錄入不規范等。例如領用包裝材料,系統要求按明細規格領用,而實際操作中卻未按規格領料,造成各明細規格產品之間包裝成本相差很大。另外,還存在隨意修改數據的情況,由于成本計算時間較長,如果修改數據不通知財務,必然會導致結果錯誤。二是系統設置問題。主要是根據公司實際情況后期開發的報表存在疏漏。三是準備工作不夠充分。雖然系統上線經過了長時間的測試,但由于僅做了流程測試,導致正式使用成本模塊時,許多操作人員數據錄入不夠認真,意識還停留在手工階段,操作隨意性很大。
由此可以看出,人員素質是影響系統能否正常運行的關鍵因素。操作人員能否嚴格按照要求進行數據錄入和相關業務操作直接影響最終計算結果。加之系統涉及部門較多,只有部門間緊密配合,才能提高效率和準確性。針對此情況公司采取了以下措施:
1.對操作人員、系統使用人員進行分批、多次培訓。培訓交流工作貫穿了系統實施上線的整個過程,參與人員包括了相關崗位的各級應用人員和管理人員,以讓大家充分掌握業務操作方法。
2.建立例會制度。由計算機中心牽頭,每周二上午召開例會,總結通報上周情況,并對本周工作作出安排。通過例會,大家共同討論問題,總結經驗,互相交流,以避免同類錯誤在不同車間多次出現。同時,通過例會討論對系統運行提出了不少意見,使系統相關設置更加合理、完善。
3.由車間、財務、計算機中心共同制定系統操作規程,對各類業務事項做出明確規定,所有系統操作人員必須認真學習并嚴格遵守。通過規范化要求,大大減少了操作的隨意性,使得計算結果更加真實、可靠。
4.建立考核制度。為了提高大家的認知意識,公司對規程操作人員實行經濟考核,這使得一部分思想意識薄弱的人員增強了責任心,杜絕人為原因造成的錯誤出現。
5.建立一整套檢查方案,從數據錄入、標準設置、倉庫盤點、費用分配、簡單成本分析等幾個方面嚴格檢查,并制定修改數據必上報制度,多方面下手,力求杜絕錯誤出現。
6.在使用系統計算成本的同時,根據系統計算的原理,同時手工再計算一遍成本。將兩種方法計算的結果進行比較,核對系統計算的正確性。經過8個月的并行計算,確定系統計算無誤后,才放棄手工計算。
(二)二次開發工作量巨大
由于系統的局限性和新華制藥生產情況的復雜性,系統并不能完全適合新華制藥的實際需求。因此,根據新華制藥的實際情況,公司對系統處理流程做了很多修正。
1.車間之間的物料領用。例如207車間生產的醋酐產品在外售的同時,207車間生產的其他產品和其他車間也要使用醋酐產品。由于207車間沒有足夠的地方儲存,必須先交公司庫再領回使用。領用醋酐產品出庫時須計算產品成本,而出庫成本需根據期初、期末和本期交庫成本加權平均計算,這就導致在計算產品入庫成本之前需先計算產品出庫成本,而沒有產品入庫成本又無法計算產品出庫成本。對此情況,公司提出,領用醋酐產品時調撥單據做上“調撥”標記,以與其他調撥單區分,同時設置該類調撥單在審核后自動加上“記賬”標記,從而禁止該類調撥單參與產品出庫核算,此類調撥單上物料單價取上期期末平均單價,如無結存則取累計平均單價,從而杜絕了死循環的出現。
2.應客戶要求和GMP(國家食品藥品監督管理局藥品認證)管理要求,有時會出現產成品返工生產情況。產成品返工生產需單獨統計,同時系統要求交庫產品不能領用自身,但如在同一月內同時出現A產品交庫和A產品返工情況時,必然會出現A產品領用A產品的結果,而此類事項系統也判斷為死循環。對此公司采取和上一種情況一樣的處理方法,在調撥單據上加“返工”標記,并在車間設置退貨倉庫。返工的產品調撥到車間退貨倉庫,并在退貨倉庫內做虛擬出入庫。例如A產品,其主要生產原料為a,出庫時產品為A,數量為實際退庫數量,入庫時產品為a,數量根據實際損耗情況填寫,但要求金額必須保持一致,然后再領用a交庫。這樣既可以杜絕死循環的出現,又可以反映返工的損耗,方便查詢,同時還便于統計返工的數量。
3.要求軟件公司提供權限管理功能。由于成本模塊涉及人員較廣,信息透明度較高,而原系統功能中并不包括相關的權限控制,這就導致非本車間(部門)人員可以隨意瀏覽本車間(部門)相關的數據、報表、BOM單等,造成機密數據泄露。針對這種情況,根據公司的要求,軟件公司開發了權限保護程序,除相關管理人員和公司領導可全部授權外,對其余人員的權限進行嚴格限制,做到車間(部門)之間不能相互瀏覽數據,車間(部門)內不同崗位(專業)不能相互瀏覽數據,從而保證了公司數據的安全性。
4.廢料回收套用成本計算也是難點,因為在交庫產品中是不包括廢料的,所以在計算成本時廢料在系統之外,這就形成了有實物無價值的情況,會造成交庫產品成本虛高,而系統又無法計算廢料的實際成本。為解決這個問題,公司在每一種產品的用料配方中都加上了廢料回收一項,并對每一種廢料編制了計劃價格,讓程序員給開了數量錄入通道,可以通過手工輸入廢料量,量是負數(原來程序是不允許輸入負數量的)。這樣在計算產品成本時,廢料會作為負數沖減交庫產品成本,同時廢料也以計劃價格作為結轉廢料銷售成本或繼續參與產品生產時價值確認的依據。
5.根據新華制藥管理經驗,二次開發相關報表。原系統中包含的報表種類較少,例如系統自帶的物料收發報表只能提供計劃金額,無法提供實際金額,這對財務工作來講無疑是一個很大的缺陷。對此,公司和軟件公司開發人員共同開發了可反映實際金額和計劃金額的物料收發明細表、原料消耗明細表、單位成本明細表、原料節約報表、產品成本報表、多月成本比較表等,滿足了管理工作的需求。
二、實施效果
醫藥、化工企業實施ERP,生產管理、成本管理是難點。其中BOM(產品配方)的配置、聯副產品成本的計算、回收品管理、多計量單位的轉換、成本核算的特殊性又是難點中的難點。在新華制藥成本模塊實施過程中,各方實施人員多次討論、測試、調整,最終開辟出一條適用于新華制藥的應用模式,取得了預期的成果。
1.生產、成本系統上線后,可以有效降低人工統計的差錯,提高準確率,進而控制人為錯誤的繼續擴大。ERP成本模塊運行后,可以隨時進行車間內部的賬物核對。因系統賬務的公開透明,促使車間對物料的管理比以前更加認真、細致,發現問題及時反饋、查找原因并及時改正,工作責任心明顯提高。這正符合GMP的“將人為錯誤縮減到最低限度”、“最大限度保證藥品質量”等要求。
2.通過查看每個產品的投料情況,可以分析出工人是否按SOP(工藝操作規程)、BPR(生產批記錄)要求規范操作,以及原輔料使用情況是否到位、產品質量與原輔料的節約情況等。通過查詢批次入庫產品領料明細,可清楚地看到單批的投料情況及單批成本。通過單批的投料對應其產品質量,可改進工藝參數,使工藝規程更完善,產品質量更穩定。同時,使監督管理工作更加細致、有據可查、有路可循。
3.使用系統提供的實際成本計算方法,材料成本的計算更加符合生產的實際情況,這樣不僅能夠真實地核算成本,為企業決策提供依據,還能及時反映出企業生產過程中存在的問題,便于企業改進生產管理。
4.系統可以提供對單個或多個物料的動態庫存查詢功能。通過對物料的現有庫存、安全庫存、預計入庫量、已分配量進行運算,得到任何時間段內的預計可用庫存情況,可隨時掌握物料的庫存狀況,輔助供應、銷售、生產、倉儲等部門進行管理決策。
5.結合新華制藥多年原料藥生產成本管理經驗開發的一系列成本考核報表,能夠多維度、強精度考核產品的生產成本,有利于將成本管理納入到考核指標體系,運用管理會計的基本原理,以分部門核算的方法建立一套包括成本、收入、費用的考核指標。可及時有效地反映各部門的收支情況,不僅便于領導的跟進、查究,更重要的是建立和強化了部門的成本約束意識和收入對比意識。