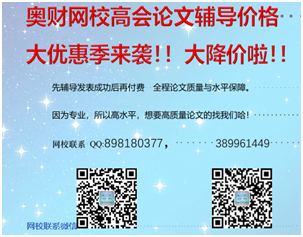
為了應對經濟全球化條件下日趨激烈的競爭局面,提高企業的長期競爭實力,戰略管理的理論與方法興起。它突破了傳統管理“正確地做事”的思維范式,而立足于“做正確的事”。這一思想深深影響了作為企業決策支持系統的管理會計,成本管理自然也不例外,從戰略角度來研究成本形成與控制的戰略成本管理(strategic cost management,SCM)應運而生。本文將對SCM的思想觀念、在這一觀念指導下的方法集以及這些觀念和方法如何在我國企業中有效推行等問題進行較為全面的探討。
一、戰略成本管理(SCM)的觀念
美國會計學界兩位著名的教授庫伯(Cooper)和斯拉莫得(Slagmulderr)對SCM曾作如下簡明的界定:SCM意指企業運用一系列成本管理方法來同時達到降低成本和加強戰略位置(improve thestrategic position of a firm)之目的[1].綜合當今SCM的思想觀念與方法,筆者認為其與傳統的成本管理相比至少具有以下特點:
l.成本管理的目的變化 SCM的目的不僅在于降低成本,更重要的是為了建立和保持企業的長期競爭優勢。也就是說企業必須探求提高(或不損壞)其競爭地位的成本降低途徑。如果某項成本降低途徑削弱了企業的戰略地位,則應棄之不用;另一方面,如果某項成本的增加有助于增加企業的競爭實力,則這種成本的增加是值得鼓勵的。如某細分市場上的顧客需要設立某項特殊的產品售后服務,雖然這一做法會增加企業成本,但它吸引了顧客,保持了企業的競爭優勢,從長遠來看利大于弊;當然企業亦可通過工程再造(reengineerin)來重組業務流程,以達到同時降低成本和強化企業的競爭地位之目的。比如某醫院通過精簡就診程序來降低成本,并且力圖使得重新設計后的就診程序有利于減輕病人的心理壓力。醫院這一舉措導致顧客增加,戰略位置加強。
2.成本管理的范圍拓展 SCM是全方位、多角度、突破企業邊界的成本管理。首先,由于當今企業成本結構中,產前與產后的成本比重逐步增加,則其成本管理不應停留在產品生產過程的耗費控制方面,更應著眼于產前的產品設計和材料采購成本、產后的產品營銷和顧客使用成本控制等方面。因而SCM深入到企業的研發、供應、生產、營銷及售后服務部門,以全面、細致地分析和控制各部門內部及各部門之間(intra-organizational)相互聯系的成本。其次,戰略成本管理范圍不局限于企業內部,還超越企業邊界進行跨組織(inter-organiza-tional)的成本管理,諸如與企業價值鏈相關的上游(供應商)與下游(分銷商)企業建立電子資料信息交換系統(EDI)、及時運輸系統,相互協調地進行成本改進。值得注意的是,在當今全球經濟一體化條件下,企業成本管理不應局限于國內而應在全球范圍內重構企業價值鏈,以獲取全球經濟的組合優勢。最后,還應對企業外部(extra-organizational)競爭對手成本信息進行推測與分析,在相互比較中找出本企業的成本差距,重塑企業的成本與競爭優勢。
3.成本管理的重點轉移 傳統成本管理重在成本節省(cost reduction),即力求在生產過程中不徒耗無謂的成本和改進工作方式以節約本將發生的成本支出,它表現為“成本維持”和“成本改善”兩種執行形式[2].減少廢品損失、節約能耗、零庫存。作業分析與改進等皆屬此列。而SCM重在成本避免(cost avoidance),立足于預防。在進行企業策劃時就對企業的地理位置、市場定位、經營規模等一系列具有源流特質的成本動因進行全面綜合的考慮,以從源頭上控制成本的發生。另外,在產品的設計與開發階段,為避免成本的發生,盡力設計滿足目標成本要求、且具有競爭力的產品。
4 .成本管理的方法更新 由于受戰略管理的思想和方法的影響,SCM的方法有別于傳統的成本管理方法。至于SCM的方法究竟有哪些,目前國內外文獻中說法不一。筆者認為,為了達到SCM的取得企業長期競爭優勢的目的,可以從以下兩個層面來創新和選擇為實現這一目的的方法:一個是戰略成本規劃(strategic costing)層面,旨在幫助企業通過事先的成本規劃與控制,從根本上改進其長期的盈利能力。這一層面的方法主要有源自戰略管理的價值鏈分析法,以及用于制定成本目標的產品生命周期成本法、目標成本規劃法等。另一個是經營改進(operational improvement)層面,旨在改善企業日常經營活動效率,落實成本規劃,繼續提高企業競爭實力。順應這一思路的方法有競爭對手成本分析法與標竿制度(benchmarking)、成本動因分析法等。當然這種區分不可能像刀切那樣清楚。事實上,在獲取企業成本優勢的過程中,這兩個層面相輔相成,同時這些方法亦是集成與整合在一起的。
二、戰略成本管理方法
(一)價值健(value-chain)分析法
這種方法由美國哈佛商學院教授邁克爾。波特首先提出。價值這里是指買方愿意為企業提供給他們的產品所支付的價格,價值活動是企業所從事的物資上的和技術上的界線分明的各項活動。波特將其劃分為基本活動和輔助活動兩大類:前者如內部后勤、生產作業等,后者如采購、人力資源管理等,二者皆可進一步劃分為若干顯著不同的具體活動[3]。VC是一系列由各種紐帶連接起來的相互依存的價值活動的集合。也就是說,VC并不是獨立活動的匯集,而是相互依存的活動構成的一個系統[4].在這一系統內各項活動之間相互聯系,即某項活動進行的方式影響其它活動的成本與效率。波特將其劃分為內部聯系和縱向聯系(企業VC與供應商、買方及購銷渠道VC之間的聯系)兩大類[5]。聯系的普遍存在意味著僅僅考察一項活動本身并不能全面理解這項活動的成本性態,同時為降低相互聯系的活動的總成本創造了機會,企業可通過協調或優化這些聯系來創建其整體成本優勢。
1.識別與優化VC的內部聯系企業VC內部的聯系體現在輔助活動與基本活動之間,如實際采購影響外購投入的質量及生產成本、檢查成本和產品質量。更多的聯系體現在各種基本活動之間,如加強對投入部件的檢查會降低后面生產工藝過程中的質量保證成本。
2.識別與協調VC的縱向聯系這一聯系存在于同一行業內部為消費者提供某種最終產品或服務的相關企業之間。上、下游與渠道企業的產品或服務特點,及其與企業VC的其它連接點能夠十分顯著地影響企業的成本。如供應商產品的適當包裝能減少企業的搬運費用,并且,改善VC的縱向聯系,將使得企業與其上、下游與渠道企業共同降低成本,提高這些相關企業的整體競爭優勢。如施樂公司(Xerox)通過計算機終端向供應商提供其生產進度表,使供應商的元器件能及時運來,這樣可同時降低雙方的庫存成本。找出和追求這種機會,需要對供應商、買方及購銷渠道的VC進行仔細研究。
3.VC重構在對各類聯系進行深入分析的基礎上,根據所處產業競爭環境的變化,企業可對其VC進行適應性重構。如可通過改變產品組合、工藝流程、服務方式與服務范圍,重新選擇VC的上游、下游與購銷渠道或調整他們之間的聯系等方式來進行VC的剪裁與重新構建,以從根本上改變其成本地位,提高其核心競爭力。
(二)產品生命周期成本(product life CycleCost)法
從生產經營者的角度來看,產品生命周期意指產品從“孕育”到“消亡”的全過程,這一過程包括如下五個階段[6]:(1)產品研究和初始設計;(2)產品開發和測試;(3)生產;(4)銷售;(5)顧客使用。產品在上述五個階段中所發生的全部耗費即產品生命周期成本。近年來,由于對環境的日益重視,有關專家認為應將產品廢置之后對環境的影響所造成的產品廢置成本考慮進來,以更全面地反映其生命周期成本。
對產品生命周期成本的全面計量與分析,目的有三:第一,幫助企業更好地計算產品的全部成本,便于企業在將產品推向市場之前,做好總體成本效益預測,以決定開發該產品是否有利可圖。第二,幫助企業根據產品生命周期成本各階段的分布狀況來確后進行成本控制的主要階段。產品的研究開發與設計階段現已成為SCM所關注的焦點。這不僅因為開發設計本身的成本很高,而且因為設計方案確定之后,導致相關的成本鎖入(locked-incost)。據專家測算,這一階段所確定的產品成本占全部成本的比例高達75%-90%之間“‘。這意味著其成本已基本確定,以后各階段只能在這一框架內進行小幅調整,成本降低余地不大。第三,由于擴大了對成本的理解范圍,有利于在產品設計階段便考慮顧客使用與產品廢置成本,以更有效地管理這些成本。
(三)目標成本規劃法(Target Costing)
如何改進產品與工序設計,在滿足市場需求及企業所期望的盈利水平的前提下,降低設計階段被鎖定的80%左右產品成本?20世紀60年代由日本豐田汽車公司發明的目標成本規劃法可擔此重任。這一方法對提高日本工業企業(尤其是汽車制造業)的經濟效益與競爭實力,立下汗馬功勞。80年代以來,這一方法被歐美許多著名的企業(如福特汽車)相繼采用,大大改進了其成本與財務狀況。 目標成本是指企業在新產品開發設計過程中,為了實現目標利潤而必須達到的成本目標值,即產品生命周期成本下的最大成本容許值。目標成本規劃法的核心工作就是制定目標成本,并且通過各種方法不斷地改進產品與工序設計,以最終使得產品的設計成本小于或等于其目標成本。這一工作需要 由包括營銷。開發與設計、采購、工程、財務與會計甚至供應商與顧客在內的設計小組或工作團隊來進行。主要操作過程如下:
1.制定目標成本由于目標成本一目標售價 一目標利潤,因此須首先制定目標售價,這需要進行市場研究,預測市場目前和將來需要的產品及其主要功能、需求量、消費者愿意支付的價格,還應了解競爭者的產品功能與價格。然后,可根據企業中長期的目標利潤計劃,并考慮對投資報酬與現金流量的期望等因素來確定目標利潤(率),由此受市場驅動(market一driven)的目標成本得以確定。
2.改進設計以達到目標成本產品之目標成本確定之后,可與公司目前的相關產品成本相比較,確定成本差距。而這一差距就是設計小組的成本降低目標,也是其所面臨的成本壓力。設計小組可把這一差距從不同的角度進行分解,如可分解為各成本要素(原材料、配件、人工等)或各部分功能的成本差距,也可按上述設計小組內的各部門(包括零部件供應商)來分解,以使成本壓力亦得以分配和傳遞,并為實現成本降低目標指明具體途徑。然后,設計小組可運用質量功能分解(QFD)、價值工程法(VE)、工程再造等方法來尋求滿足要求的產品與工序設計方案。 QFD旨在識別顧客需求,并比較分析其與設計小組計劃滿足的需求的差距,以支持VE工程的設計過程。VE是一種評價與改進設計方案、提高產品價值的系統性方法,可通過下述兩種方式實現成本降低目標:其一,在保證產品功能的前提下,削減其零部件成本和制造成本;其二,通過削減不必要的產品功能來降低成本。工程再造通過對已設計的或已存在的加工過程進行再設計,以期進一步降低成本。
(四)競爭對手成本分析法和標率制度(Benchmarking)
在進行競爭對手成本分析時,必須首先從各種渠道獲知大量相關信息,初步估計競爭對手的各項成本指標,如找出競爭對手的供應商,以及他們提供的零部件的成本;分析競爭對手的人工成本及其效率;評估競爭對手的資產狀態及其利用能力等。可采用拆卸分析法(tear-down analysis)將競爭對手的產品分解為零部件,以明確產品的功能與設計特點,推斷產品的生產過程,對產品成本進行深入了解。另外還須根據對手其它信息來調整上述估計指標,如競爭對手現在及未來戰略及其所導致的成本水平變化、企業環境的新趨勢以及產業的潛在進入者的行為。當競爭對手的成本結構的可接受的估計被確定下來之后,公司可以使用這一成本信息作為計量其自身成本業績的標竿(benchmark),即以此作為目標和尺度來進行系統的、有組織的學習與超越。這一分析方法提供了公司與最佳業績者之間的現在和未來的成本差異,反映了公司所處的相對位置,并指出了改進的具體目標與途徑,在削減成本的同時使企業的產品和過程特性得以改進,戰略位置得到加強。