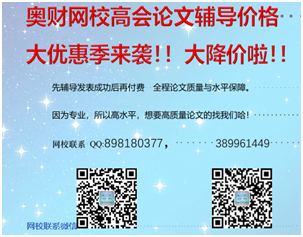
精益管理源于精益生產。精益生產(LP—Lean Production)又稱精良生產,是美國麻省理工學院教授詹姆斯.P.沃麥克等專家通過“國際汽車計劃(IMVP)”研究項目中提出來的。精益生產是一種生產管理技術,它能夠大幅度減少閑置時間、作業切換時間、庫存低劣品質、不合格的供應商、產品開發設計周期以及不及格的績效,也就是要求不斷消除各種形式的消費,取消那些不增加產品價值的工作。
在現代企業管理中,精益管理由最初的在生產系統的管理實踐成功,已經逐步延伸到企業的各項管理業務,也由最初的具體業務管理方法,上升為戰略管理理念。它能夠通過提高顧客滿意度、降低成本、提高質量、加快流程速度和改善資本投入,使股東價值實現最大化。
杭州朝陽橡膠有限公司創建于1998年4月,2000年3月20日,第一期30萬套全鋼子午線輪胎生產線開工。公司主要生產高性能全鋼絲載重子午胎系列產品,經過不懈努力,公司實現了高速發展。目前具有全國一流的全鋼子午胎生產線和17大系列51種規格,公司營運規模大,2011年公司完成總產值97.47億元,完成全鋼子午胎產量615.89萬條。
近年來,全鋼子午胎產能急劇擴張,直接導致供過于求的狀態,國際范圍內的競爭也日益加劇,與此同時,隨著技術門檻的逐漸降低,低成本競爭者還在持續涌現。隨著中國企業和外國企業在中國本土展開競爭,國內企業原有的人工成本優勢已不復存在,公司要生存必須轉變觀念,通過管理革新來應對挑戰,而實施精益管理、消除浪費是提高企業競爭力的重要手段。
在企業里不增加價值的活動,或盡管是增加價值的活動,但所用的資源超過了“絕對最少”的界限,也是浪費。而精益管理要求企業的各項活動都必須運用“精益思維” (Lean Thinking),以最小資源投入,包括人力、設備、資金、材料、時間和空間,創造出盡可能多的價值,為顧客提供新產品和及時的服務,通過精益管理可以極大的消除浪費、提升企業競爭力。
一、公司現場存在的問題
1、制品的高庫存與脫節停產并存
目前公司生產過程中在制品庫存非常高,一方面橡膠制品工藝上要求生產后要停放4-8小時,同時各工序為避免制品脫節現象的發生,不斷增加安全庫存,從而造成在制品庫存大,現場物流混亂,過期制品多,不合格品批量產生等現象屢屢發生。與此同時生產脫節現象經常發生,造成很大的浪費。
2、生產效率較低
目前配置了5000余名員工,與國外先進企業相比至少多了一千多人。但員工看似都很忙,每天都在反映“很忙”、“人手不夠”。工序設置不夠合理,重復搬運現象較多。
3、缺乏改善動力
公司成立以來每年產量增長在30%以上,公司主要圍繞著如何擴大生產規模來開展各項工作,擴產過程中較少采用“精益思維”的模式,內部管理提升方面相對滯后,浪費現象較為普遍。同時,對于現場存在的各種浪費,員工習以為常見,缺乏改善的主動性。
二、公司原有管理模式存在的缺點
目前公司生產主要是采用生產計劃處下達總計劃,各分廠生產調度通過每天對制品庫存進行盤存,結合后道工序的需求編制下達作業計劃,操作工依據作業計劃確定的規格和數量按順序生產,當后道工序發現制品脫節時馬上通知生產調度調整計劃,信息流與物流是分開的。由于連續生產,調度無法準確盤存導致計劃安排不準確,同時生產過程中實際情況千變萬化,調度很難對所有情況均能做出及時有效的反應。
員工操作動作五花八門,主要是通過師傅帶徒弟的方式進行員工培訓,無標準化操作指導書。很多時候員工“在動著”,但并沒有“在工作著”,看似非常忙實則無用功很多,效率低下。同時生產工序設置初期缺乏工序分析,布局不夠合理。
改善活動主要靠員工自發行為,缺少組織保障,未設立相應的指標并進行分解同時激勵政策缺失,員工并沒有把改善作為日常工作的一部分,沒有形成日日改善、天天創新的改善文化。
三、有效推行精益管理來消除浪費
公司要更好地生存與發展必須推行精益管理,通過全員參與持續改善消除企業存在的各種浪費,依據公司的實際情況,從以下幾方面來推行精益管理:
1、轉變生產方式,推行看板管理
看板是一種能夠調節和控制在必要時間生產出必要產品的管理手段。它通常是一種卡片,上面記載有零部件型號、取貨地點、送貨地點、數量、工位器具型號及盛放量等信息,生產以此作為取貨、運輸和生產的指令。遵循內部用戶原則,把用戶的需要作為生產的依據。傳統生產采用上道工序向下道工序送貨,加工過程由第一道工序向最后一道工序推進,因而被稱為“推動式”生產,看板生產則采用“拉動式”,由后道工序向前道工序取貨,一道一道的由后向前傳送指令。
實現看板生產的方法因產品特性和生產條件的不同而不同,但它們的原理是一樣的。以圖1所示的情況為例,看板生產的流程有以下6個步驟:1)工序B接到生產看板;2)工序B憑取貨看板和空的料箱Ⅰ到工序A處取貨;3)工序B將裝滿所需零件的料箱Ⅱ上的生產看板取下,和取貨看板核對后,將生產看板放入工序A的生產看板收集箱內,取貨看板則掛到料箱Ⅱ上;4)工序B將料箱Ⅱ取走,并將料箱Ⅰ放到料箱Ⅱ原處的位置;5)工序B開始按生產看板上的要求進行生產;6)工序A接到生產看板后,去其前道工序取貨。
通過推看板管理,看板隨物流而動,使信息流融于物流之中,使生產活動的信息反饋及時、高效。通過看板管理實現全員生產管理,員工即時掌握下工序對制品需求的先后順序,實現準時生產,消除盲目生產,有效的降低庫存。同時質量在生產過程中得到控制,使生產過程中許多問題暴露出來,促使企業不斷改善。